在注塑模具的設計過程中,除了注塑模具的結構設計外,每個部件的材料選擇也是一項非常重要的工作,它直接影響注塑模具的使用壽命、加工成本和質量。的塑料零件。成型質量。模具的工作類型是選擇模具材料的主要依據。
In the design process of injection mold, in addition to the structural design of injection mold, the material selection of each component is also a very important work, which directly affects the service life, processing cost and quality of injection mold. Plastic parts. Forming quality. The working type of die is the main basis for selecting die materials.
由于塑料原料、產品生產細度、工作條件和質量要求的不同,注塑模具的工作條件也有很大的不同。因此,在選擇注塑模具材料時,需要從經濟和技術兩方面綜合考慮。從經濟角度看,對于大批量生產的塑件,無論使用何種塑料,工藝條件如何,成型質量有多高,通常都應采用較好的模具材料和必要的熱處理或其他強化措施。加以選擇,從而使此類模具具有較長的使用壽命。
Due to the different plastic raw materials, product production fineness, working conditions and quality requirements, the working conditions of injection mold are also very different. Therefore, when selecting injection mold materials, we need to consider both economic and technical aspects. From an economic point of view, for mass-produced plastic parts, no matter what kind of plastic is used, what the process conditions are, and how high the forming quality is, better mold materials and necessary heat treatment or other strengthening measures should be adopted. So as to make such molds have a long service life.
注塑模具一般在一定的溫度和壓力下工作。普通熱塑性塑料注塑模具的工作溫度通常在150℃以下,模腔成型壓力為25~50MPa。熱塑性工程塑料精密注塑時,模腔壓力有時可達100MPa以上;而熱固性塑料注射成型模具的工作溫度通常為150~220℃,模腔成型壓力為30~80MPa。
Injection mold usually works under certain temperature and pressure. The working temperature of ordinary thermoplastic injection mold is usually below 150 ℃, and the molding pressure of mold cavity is 25~50mpa. When thermoplastic engineering plastics are precisely injected, the cavity pressure can sometimes reach more than 100MPa; The working temperature of thermosetting plastic injection molding mold is usually 150~220 ℃, and the molding pressure of mold cavity is 30~80mpa.
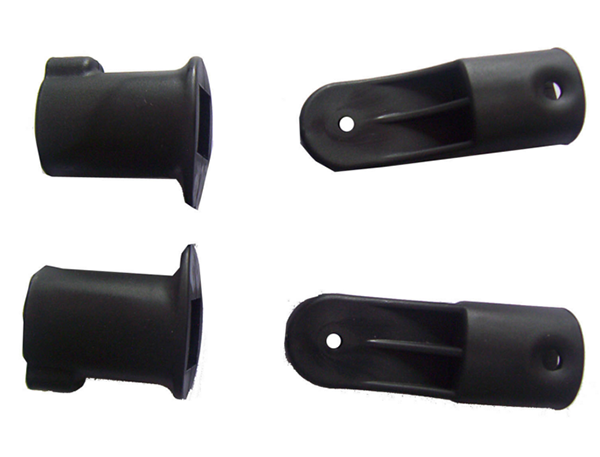
在注射過程中,模具型腔、型芯和澆注系統(tǒng)都受到流動摩擦和沖擊,因為熔融塑料被填充。在脫模過程中,模具型腔和澆注系統(tǒng)也受到固化塑件和澆注系統(tǒng)冷凝水的刮擦,會導致模具型腔、型芯和澆注系統(tǒng)面壁產生一定程度的損壞。磨損,特別是用玻璃纖維等硬質填料成型塑料件時,磨損現象更為嚴重。
During the injection process, the mold cavity, core and gating system are subject to flow friction and impact because the molten plastic is filled. In the process of demoulding, the mold cavity and gating system are also scratched by the solidified plastic parts and the condensate of the gating system, which will lead to a certain degree of damage to the mold cavity, core and the surface wall of the gating system. Wear, especially when plastic parts are molded with hard fillers such as glass fiber, is more serious.
濟南注塑加工廠家提醒,在注塑某些類型的塑料件時,注塑模具在工作過程中有時會受到腐蝕,即塑料在高溫下分解,分解出揮發(fā)性腐蝕性氣體到模具型腔、型芯和模具中。澆注系統(tǒng)的表面壁具有腐蝕作用。例如,在成型聚氯乙烯塑料、聚甲醛塑料、氟塑料、阻燃或難燃塑料時,在高溫下分解的HCl、SO2、HF等氣體對注塑模具有腐蝕作用。因此,在成型不同的塑件時,必須綜合考慮不同的工況。
Jinan injection molding manufacturers remind that during the injection of certain types of plastic parts, the injection mold will sometimes be corroded during the working process, that is, the plastic will decompose at high temperature and decompose volatile corrosive gases into the mold cavity, core and mold. The surface wall of the gating system is corrosive. For example, when forming PVC plastics, polyoxymethylene plastics, fluoroplastics, flame-retardant or flame-retardant plastics, HCl, SO2, HF and other gases decomposed at high temperature have a corrosive effect on the injection mold. Therefore, different working conditions must be comprehensively considered when forming different plastic parts.
The above is the relevant content of the answer to the question. I hope it can help you. If you have any questions about this issue, you are welcome to follow our website http://m.airindiapackersmovers.com And consult our staff, we will serve you wholeheartedly.